Advanced Collaborative Multifunctional End-Effector (ACME)
Drilling is a fundamental operation in aerospace manufacturing, significantly impacting production efficiency, quality, and safety. ACME addresses key industry challenges in automated drilling by integrating lightweight design, collaborative robot (cobot) compatibility, precise positional control, and advanced vibration suppression capabilities.
2022-2024
Company:
Year:
National Research Council Canada (NRC)
Skills:
Design and Prototyping, DFMA, Control, Kinematic and Dynamic Modelling, Programming, GUI Development
Abstract
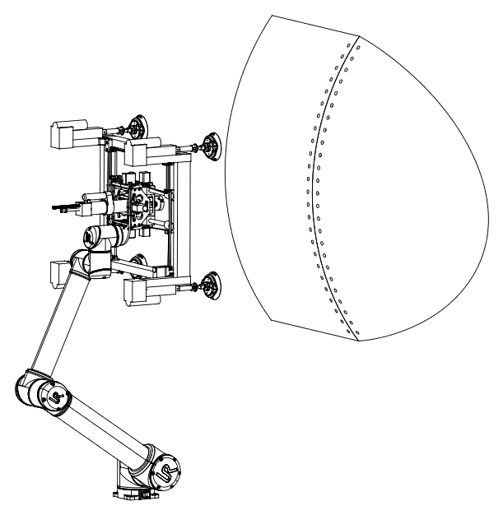
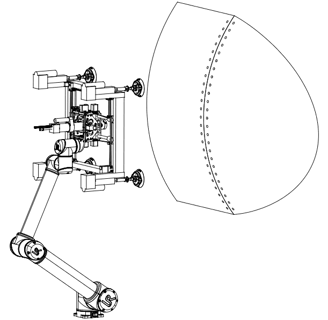
Motivation
The drilling operation is one of the most dominant manufacturing processes in aircraft assembly.
Ex. Around one million holes are drilled for rivets and fasteners in an A220.
Still, a considerable portion of drilling is done manually, which has its downsides.
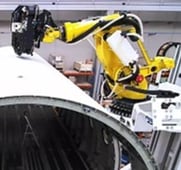
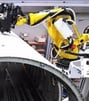
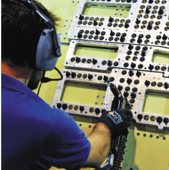

Automated Drilling
Higher productivity
A smaller number of operators
Capable of providing accurate, repeatable results
Manual Drilling
Time and labour-intensive
Musculoskeletal problems
Requires a large number of jigs
Not flexible to engineering changes
Challenges in Automated Drilling
Safety
Large capital and time investments for adoption
Over $2 million for each unit of Kuka + ALEMA drilling unit
Disruption to the factory floor layouts
Obtaining tight aerospace manufacturing tolerances
System Design
Specifications:
5 DoF drilling tool for cobots
Provides clamping force up to 100 kg by attaching the surface using suction cups
Double curvature surfaces (up to 2m in radius) with normality compensation
Onboard sensors
Camera for localization
Loadcell for clamping force control
Encoders for accurate positioning
Clamping Force:
Clamping force is achieved by moving the frame towards the surface and contacting the drilling nose with it.
The Pressure builds up and is monitored (force control) using a hole-through load cell at the nose.
Normalization Mechanism:
Self-normalization based on reaction forces on the nose (Any clamping force above 560 N will normalize the nose to the surface automatically)
Active joints (A&B) with servo motors + absolute encoders can also be utilized.
Clamping Mechanism
CoreXY Mechanism illustration
XY Positioning:
The CoreXY mechanism reduces the number of moving parts (minimum inertia) for accurate and fast positioning.
The XYZ is controlled using absolute magnetic encoders for accurate positioning.
Mechatronic Components
All the mechatronic components serve to achieve the sequence of drilling.
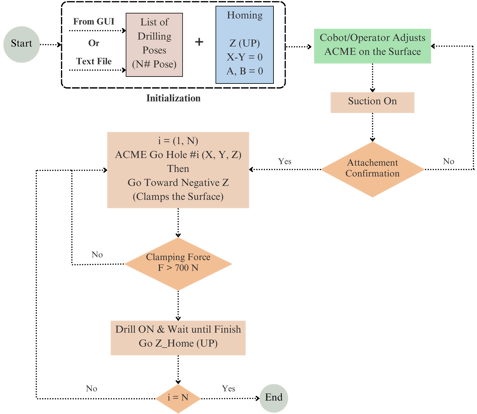
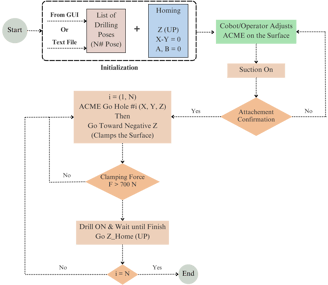
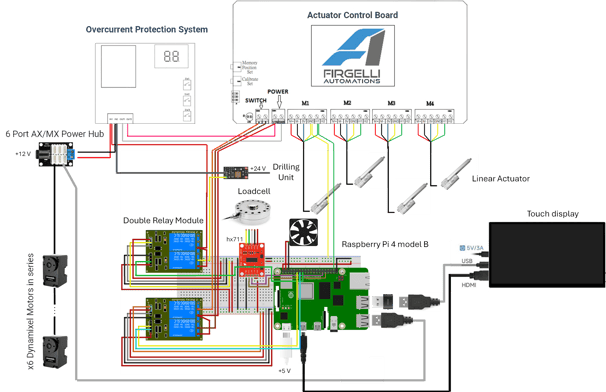
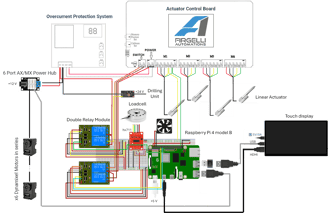
Layout of the electronics components and control box
Layout of pneumatic circuit
Drilling Sequence
The layout of the electronics and control box helps with proper assembly, installation, and maintenance
Pneumatic system provides suction for attachment and powers the drilling unit. It is controlled by the main controller (Raspberry Pi GPIO) with relay modules for digital ON/OFF control of suction and drilling units, employing serial communication protocols and feedback loops for precise operational timing and enhanced reliability.
ACME in Operation
Portfolio
Showcasing my Mechatronics Engineering experience and projects.
Contact
© 2025. All rights reserved.