Robot Geometric Calibration
Abstract
Robotic accuracy plays a pivotal role in industrial applications, particularly in high-precision tasks such as aerospace manufacturing and inspection. Inaccuracies due to manufacturing tolerances, assembly errors, joint backlash, and wear should be enhanced by employing a comprehensive calibration process.
2024-2025
Company:
Year:
National Research Council Canada (NRC)
Skills:
Kinematics Modelling, MATLAB, Simulink
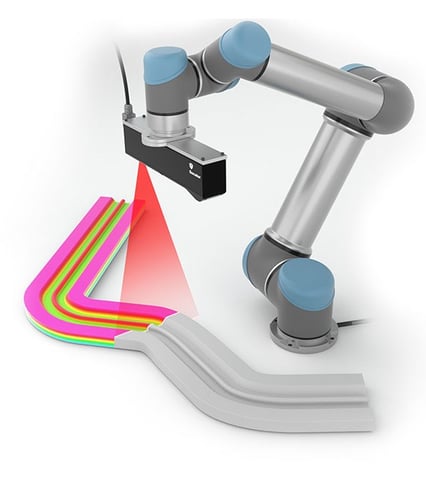

Sensor
Using an unknown artifact and the LMI High-Resolution Smart 3D Laser Line Profilers 2430, non-contact measurements of the robot end-effector's distance from an artifact along predefined paths are developed, enabling precise evaluation and adjustment of the robot's Denavit-Hartenberg (DH) parameters.
The Laser Line Profiler is an exceptional tool for this application due to its non-contact, high-precision measurement capabilities. Its compact design and ease of integration make it ideal for robot-mounted applications. The profiler provides dense point cloud data with sub-millimetre accuracy, enabling precise identification of kinematic discrepancies. Unlike traditional calibration methods that rely on external and often costly equipment, this integrated approach streamlines the process and enhances efficiency.


Stages of Robot Geometric Calibration
Established methodologies, the calibration process is structured into the following stages:
Modelling: A mathematical model is developed to define the robot's kinematic structure using the Modified Denavit-Hartenberg (MDH) parameters. This ensures an accurate representation of the robot's geometry, including the tool and world frames.
Measurement: The LMI 2430 profiler measures distances from the end-effector to the artifact across a range of poses.
Error Identification: Errors in the robot's DH parameters are identified by comparing measured poses with theoretical ones derived from the kinematic model. Optimization algorithms minimize the discrepancies.
Compensation: Adjustments are made to the robot's model to incorporate the identified errors. These updates improve path planning accuracy and enhance the robot's overall performance.
Validation: The updated model's accuracy is being tested through repeatability and positional error assessments in the workspace.
Portfolio
Showcasing my Mechatronics Engineering experience and projects.
Contact
© 2025. All rights reserved.